Why Commercial Framing With Wood Saves 40% on Construction Costs
- Set square Construction
- Dec 20, 2024
- 8 min read
Updated: Jan 5
Rising construction costs continue to challenge commercial property developers across North America. However, we've discovered that commercial framing with wood consistently delivers up to 40% cost savings compared to traditional materials like steel and concrete.
As experienced commercial framing contractors in Vancouver, we've witnessed firsthand how modern wood construction has evolved. In fact, today's engineered wood products offer remarkable structural performance while significantly reducing wood framing cost per square foot. Through our extensive experience as a commercial framing contractor, we've helped numerous clients achieve substantial savings without compromising on quality or safety.
We'll explore how modern wood framing technology, combined with advanced engineering techniques, creates these impressive cost benefits while meeting all building code requirements. We'll also examine the specific factors that contribute to these savings, from material costs to construction timelines.
Understanding Modern Commercial Wood Framing Technology
As commercial framing contractors, we've witnessed remarkable advancements in wood construction technology over the past decade. Our experience with modern wood framing techniques has shown us how engineered wood products are reshaping the commercial construction landscape.
Advances in engineered wood products
At the forefront of our projects, we utilize cutting-edge engineered wood products that deliver exceptional results. These materials include:
Laminated Veneer Lumber (LVL) for superior load-bearing applications
I-joists for efficient floor and roof systems
Cross-laminated timber (CLT) for larger structural elements
Oriented Strand Board (OSB) for versatile sheathing solutions
Furthermore, these engineered products have proven to leave 75% less carbon footprint than concrete or steel, making them an environmentally conscious choice for our clients.
Structural performance improvements
Throughout our years as commercial framing contractors in Vancouver, we've seen firsthand how advanced framing techniques have enhanced building performance. By implementing optimum value engineering (OVE), we've achieved up to 30% reduction in framing material costs. Additionally, our advanced framing methods create deeper, wider insulation cavities compared to conventional approaches, substantially improving the whole-wall R-value.
Modern building code compliance
Presently, we're excited about the recent changes in building codes that have expanded the possibilities for wood construction. The National Building Code now permits encapsulated mass timber construction up to 12 storeys, opening new opportunities for our clients. Moreover, our advanced framing techniques fully comply with current building codes while delivering structures that are more resource-efficient than conventional framing.
In our experience, modern wood frame construction excels in meeting technical requirements for design and construction. Consequently, when properly constructed with wood structural panels, our walls provide the strength needed to safely withstand design loads. Through our commitment to innovation, we ensure that every project not only meets but exceeds current building code standards for structural integrity and fire protection.
Breaking Down the 40% Cost Savings
Through our extensive experience as commercial framing contractors, we've consistently observed substantial cost advantages when using wood construction methods. Initially, let's examine exactly how these savings break down across different aspects of construction.
Material cost comparison with steel and concrete
In our day-to-day operations, we've found that wood consistently proves more economical as a primary building material. Wood's inherent affordability as opposed to steel and concrete results in lower upfront material costs. Notably, our projects demonstrate that wood's natural abundance and simpler processing requirements contribute to these cost advantages.
Labor cost reductions
As a result of our refined prefabrication processes, we've achieved remarkable labor cost efficiencies. Our data shows that wood construction typically requires smaller crews since components arrive pre-fabricated with joints already cut. Subsequently, this streamlined approach translates into substantial labor savings, particularly because the prefabricated components fit together seamlessly, reducing on-site labor time.
Equipment and machinery savings
Perhaps one of the most overlooked advantages we've discovered is the reduction in equipment-related expenses. Since wood is lighter than traditional materials, we require less sophisticated tools and machinery for transportation and installation. Particularly noteworthy is the impact on foundation requirements - wood's lighter weight means we can design smaller foundations, reducing both concrete usage and reinforcement needs.
From our perspective as commercial framing contractors in Vancouver, these cost benefits stem from several key factors:
Material costs are generally 30% lower for floor and wall framing
Foundation requirements are minimized due to wood's lighter weight
Construction equipment needs are less extensive
Labor crews can be smaller without sacrificing efficiency
Throughout our years in commercial framing, we've observed that the overall project costs typically benefit from wood construction's holistic advantages. Rather than focusing solely on material prices, we consider the entire cost structure, including installation speed and structural requirements, to deliver maximum value to our clients.
Accelerated Construction Timeline Benefits
Time efficiency stands at the forefront of our commercial framing projects in Vancouver. Throughout our years of experience, we've witnessed firsthand how modern wood construction methods dramatically accelerate project timelines.
Prefabrication advantages
In our controlled factory environment, we've consistently achieved remarkable efficiency gains. According to our project data, factory-built construction reduces overall project completion time by up to 50% while simultaneously cutting costs by 20% or more. Specifically, we've found that prefabrication enables us to begin framing work while foundation construction proceeds on site, creating a seamless workflow that maximizes productivity.
Reduced foundation requirements
One of the most notable advantages we've discovered is that wood components are considerably lighter than traditional materials. This characteristic allows for speedier installation and requires fewer people on site. Our experience shows that prefabricated components can be assembled with smaller crews, which simultaneously limits work stoppages and increases overall productivity.
Faster assembly processes
The efficiency of our assembly process is particularly evident in our recent projects. For instance, in our student housing projects, we've documented that each prefabricated dorm room takes merely 14 days to complete - approximately 50% faster than conventional construction methods. Our sophisticated 3D modeling and digital software enable us to meticulously plan each phase, from concept through completion.
We've optimized our process to include these time-saving elements:
Just-in-time delivery system that minimizes site storage requirements
Weather-resistant manufacturing environment that eliminates climate-related delays
Simultaneous construction of multiple building components
Pre-planned assembly sequences that reduce on-site coordination time
The impact of these efficiencies becomes clear in our real-world applications. Throughout our commercial framing projects, we've observed that prefabricated frames can often be assembled within days, unlike the weeks required for traditional on-site construction. This acceleration in timeline translates directly into earlier occupancy dates, allowing our clients to begin generating returns on their investments sooner.
Engineering and Design Flexibility
In our decades of experience as commercial framing contractors, we've discovered that wood's engineering versatility sets it apart from other building materials. Notably, our projects showcase how modern wood construction combines strength with remarkable design flexibility.
Spanning capabilities and load-bearing strength
We've consistently achieved impressive results with wood's structural capabilities in our commercial projects. Our engineering team has successfully implemented wood framing systems that demonstrate the highest strength-per-weight ratio of any building material. Essentially, this allows us to create larger, more open spaces while maintaining structural integrity.
Through our innovative approach to commercial framing, we've developed methods to enhance spanning capabilities even further. In cases requiring extended spans, we've perfected a technique of splitting timber and incorporating steel I-beams within the wood structure, preserving the natural timber esthetic while boosting structural performance.
Adaptation to complex architectural designs
Our expertise in wood framing has enabled us to tackle increasingly complex architectural challenges. The inherent adaptability of light wood framing makes it ideal for customizing projects of various scales. We've found that wood's natural properties allow us to:
Create custom configurations for specific site conditions
Design flexible interior spaces with movable partitions
Accommodate various soil conditions and site requirements
Integrate complex geometric features
Adapt to challenging property gradients
Integration with other building systems
Throughout our commercial framing projects, we've mastered the art of seamlessly incorporating wood structures with other building systems. The versatility of wood allows us to mix and match elements to achieve the precise level of customization needed for each project. Undoubtedly, one of our greatest strengths lies in our ability to manufacture customized components off-site while construction progresses, helping meet crucial project milestones.
We've primarily focused on developing solutions that maximize wood's natural advantages. For instance, wood's cellular structure creates air pockets that enhance insulation properties. Furthermore, our framing techniques facilitate the easy integration of insulation materials into wall cavities, significantly improving overall building energy efficiency.
In our recent commercial projects, we've successfully implemented advanced prefabrication techniques that allow for precise customization of products needed for each site. This approach not only ensures accurate fits but also enables parallel manufacturing processes that align perfectly with construction timelines. Through careful planning and execution, we've consistently delivered projects that showcase wood's remarkable ability to adapt to modern building requirements while maintaining its traditional appeal.
Risk Management and Insurance Considerations
Safety and risk management remain at the heart of our commercial framing operations. Throughout our years serving Vancouver's construction industry, we've developed comprehensive strategies to address these crucial aspects of wood construction.
Fire resistance ratings
Our commitment to fire safety shapes every project we undertake. The National Building Code defines fire-resistance rating as the time period materials withstand flame passage and heat transmission under specific test conditions. Essentially, our wood-frame assemblies undergo rigorous testing to meet these standards. Through careful design and implementation, we ensure our structures achieve the necessary fire-resistance ratings through proven techniques such as encapsulation, charring layers, and fire-retardant coatings.
Notably, our approach to fire safety encompasses multiple layers of protection. The stability of our wood-framed structures primarily relies on meticulously designed connections between components, utilizing specialized hardware such as nails, screws, and metal plates. These connections prove vital in maintaining structural integrity during challenging conditions, especially in the event of fire exposure.
Structural integrity guarantees
Throughout our projects, we implement rigorous quality control measures to guarantee structural performance. Our wood members demonstrate an inherent fire resistance thanks to their slow burning rate of approximately 0.6 mm/minute under standard fire test conditions. The char layer that forms during exposure actually protects the unburned portion of the wood, allowing our structures to maintain their integrity for extended periods.
The effectiveness of our structural design is evident in the statistics - merely 1% of concrete buildings face demolition due to fire damage, whereas this figure stands at 8% for wood frame buildings. Nonetheless, we address this disparity through comprehensive fire protection systems and careful attention to moisture control, which remains crucial for maintaining long-term structural integrity.
Insurance premium impacts
We maintain complete transparency regarding insurance considerations for our projects. Insurance rates for wood frame construction typically range from 5 to 6 cents per CAD 139.34 value per month. These rates reflect various risk factors that insurers evaluate:
Fire prevention measures
Building envelope protection
Materials quality assurance
Contractor experience levels
Site security practices
The insurance landscape presents certain challenges, with builders' risk insurance rates showing notable differences between wood and concrete structures. Current data indicates rates of CAD 0.01 for concrete and CAD 0.07 for wood per CAD 139.34 monthly. This differential primarily stems from factors such as fire peril and moisture risk management.
To mitigate these insurance impacts, we've implemented sophisticated moisture and mold mitigation strategies. Our established moisture control protocols help prevent costly rework and maintain the integrity of our structures. The importance of proper moisture management has emerged as one of the most significant considerations in insurance rate setting.
By prioritizing these critical aspects of risk management, we continue delivering successful commercial framing projects that meet both safety standards and insurance requirements. Our experience has shown that through proper planning and execution, wood frame construction can achieve remarkable performance while maintaining reasonable insurance costs.
Conclusion
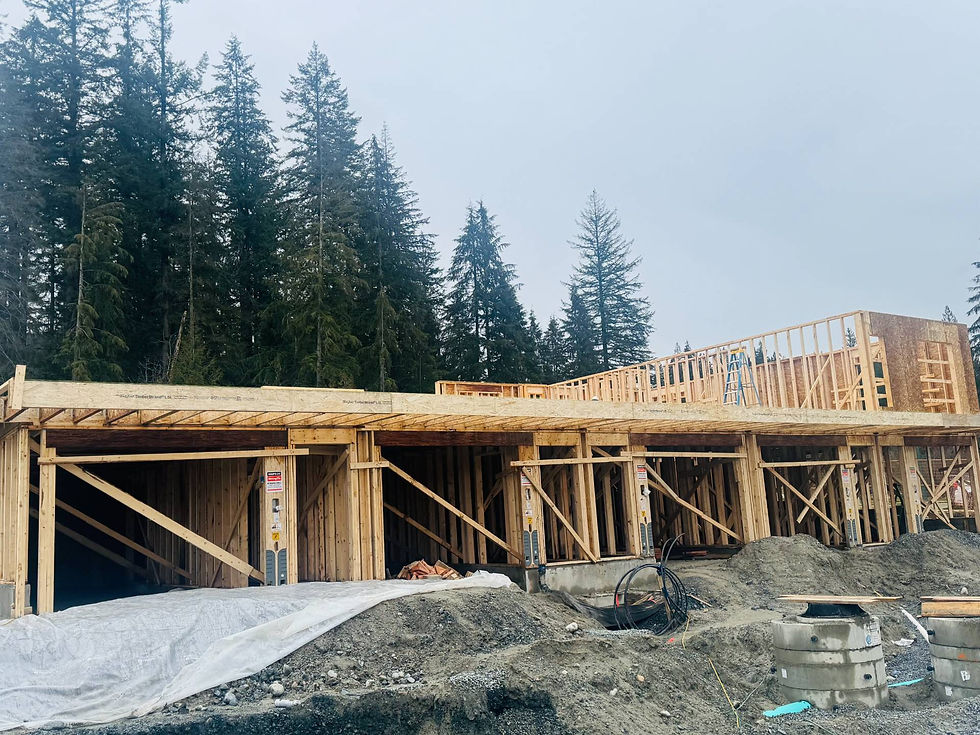
Throughout our years as commercial framing contractors in Vancouver, we've consistently proven that wood construction delivers remarkable cost benefits while meeting rigorous safety and performance standards. Modern engineered wood products, combined with our advanced construction techniques, create buildings that stand the test of time while saving our clients up to 40% on construction costs.
Our experience shows that wood framing excels beyond just cost savings. Faster construction timelines, enhanced design flexibility, and superior environmental performance make wood an ideal choice for commercial projects. Though insurance considerations require careful attention, our proven risk management strategies and moisture control protocols effectively address these challenges.
Wood construction represents the future of commercial building. As building codes evolve and technology advances, we continue refining our methods to deliver even greater value. Rather than viewing wood as simply an alternative to steel or concrete, we see it as the primary solution for creating sustainable, cost-effective commercial structures that serve our clients' needs while protecting their bottom line.
Comments